Download as pdf

Client Background
Terumo Yamaguchi Corporation, a subsidiary of the global healthcare leader Terumo Corporation, manufactures high-quality medical devices and pharmaceutical products. Their production process requires the use of ethylene oxide (EtO) for sterilisation — a highly effective but hazardous compound that demands strict emission control.
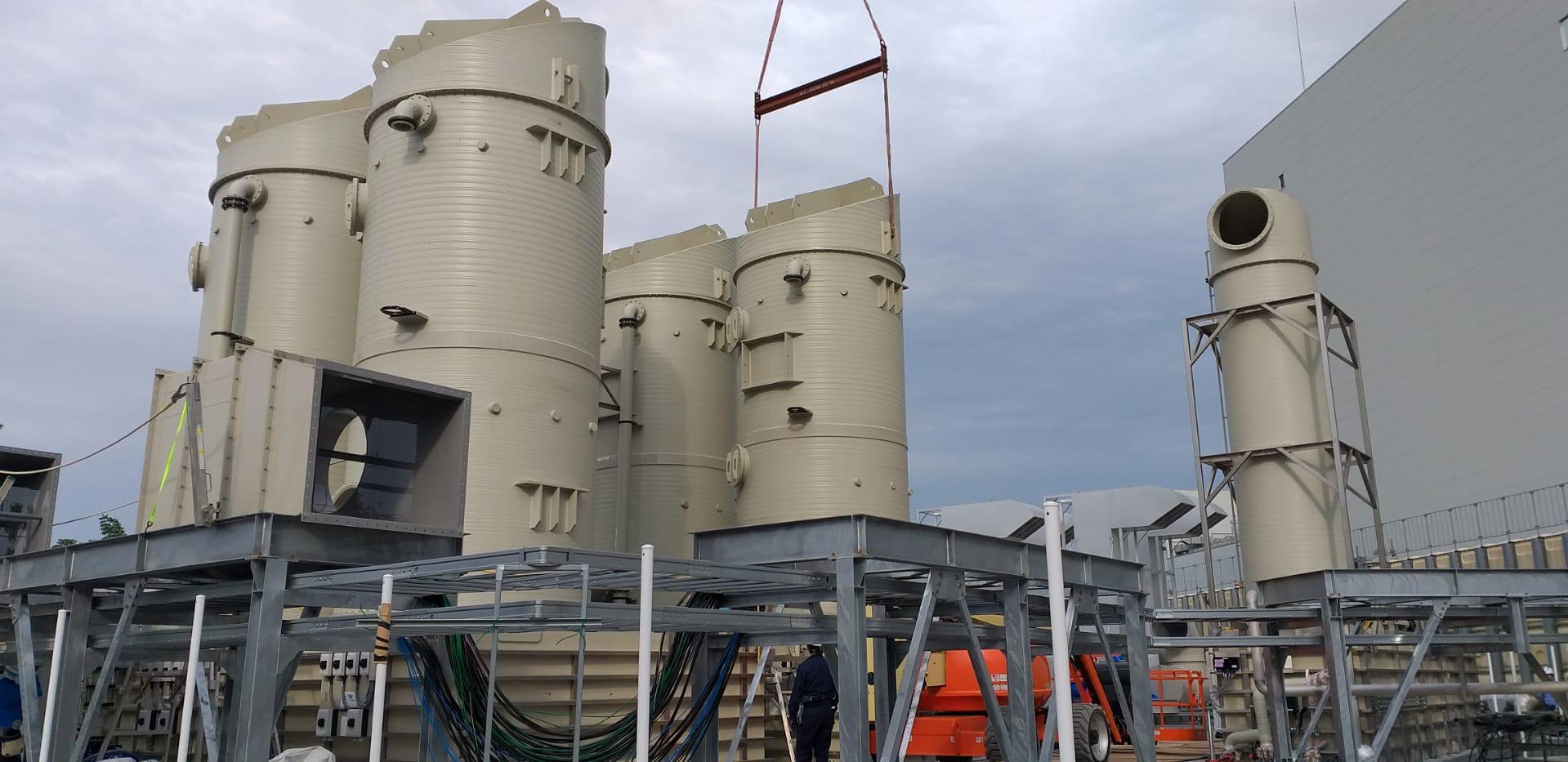
Project Objective
To design and implement an advanced emission abatement system capable of treating two very different EtO airflows:
A low-flow, high-concentration stream from the sterilisation chambers
A high-flow, low-concentration stream from the aeration rooms
The solution needed to achieve high removal efficiency, handle fluctuating flows, and be compact enough for international shipment and plug-and-play installation.
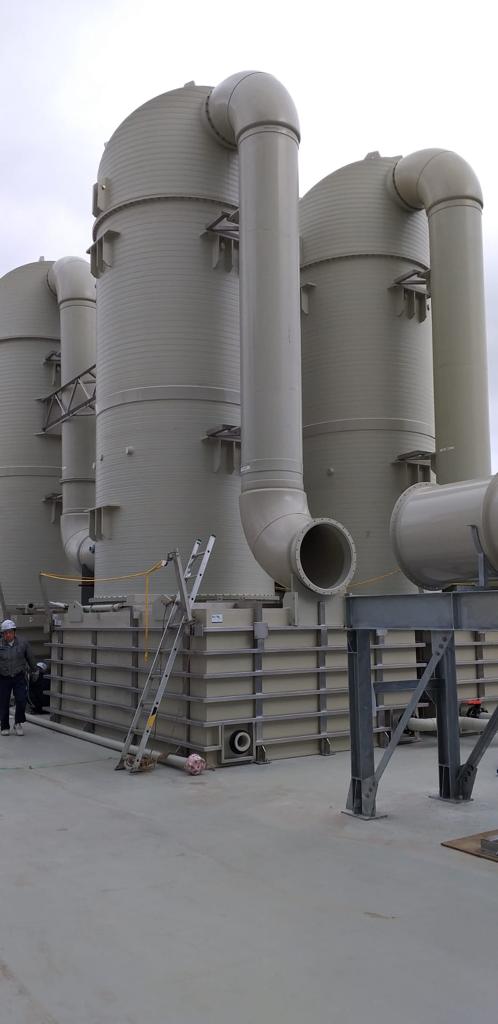
Challenges
Treating EtO emissions effectively is always a technical challenge — but in this case, the difficulty was compounded by the dual nature of the emission sources and the international logistics involved.
On the one hand, the scrubber had to manage intermittent, high-concentration gas from sterilisation chambers. On the other, it needed to process a continuous, high-volume airflow from aeration rooms with much lower EtO levels. These dynamic and fluctuating conditions made it crucial to engineer a solution that could perform consistently and within environmental regulations — all while being compact and modular enough to ship from Belgium to Japan.
Key challenges included:
Dual emission sources with drastically different flow and concentration profiles
Meeting strict environmental compliance targets
Managing inconsistent, discontinuous gas flows without compromising performance
Ensuring smooth overseas transport and on-site integration
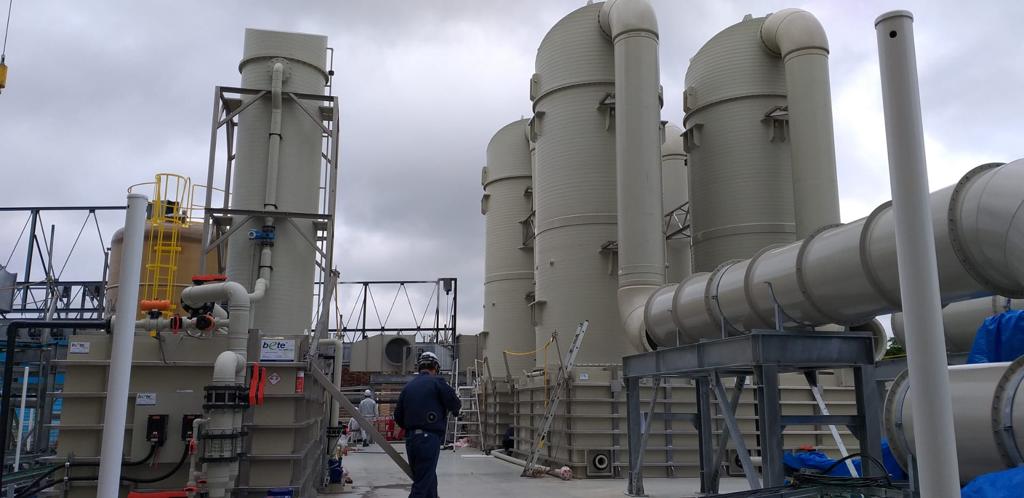
Trevi’s Solution
Trevi designed and built a custom three-stage acid wet scrubber, engineered for the complex needs of the Yamaguchi site:
Stage 1: Treats concentrated emissions directly from the sterilisation chambers
Stage 2: Integrates the high-volume air from aeration rooms
Stage 3: Polishes the remaining air to ensure maximum EtO removal
The system was designed for long-term reliability, minimal maintenance, and stable performance under fluctuating conditions.
Results
Achieved 99.66% EtO removal efficiency
Compact system enabled smooth delivery and on-site installation
Fully compliant with Japanese environmental standards
Reliable performance across varying operational conditions
Key Project Specs
Parameter | Value |
Max flow rate | 650 m³/min |
Sterilisation chambers | 50 m³/min @ 747 kg/day EtO |
Aeration rooms | 600 m³/min @ 30 ppmv EtO |
Technology | Acid wet scrubber (3-stage) |
Location | Yamaguchi, Japan |
Completion Year | 2018 |
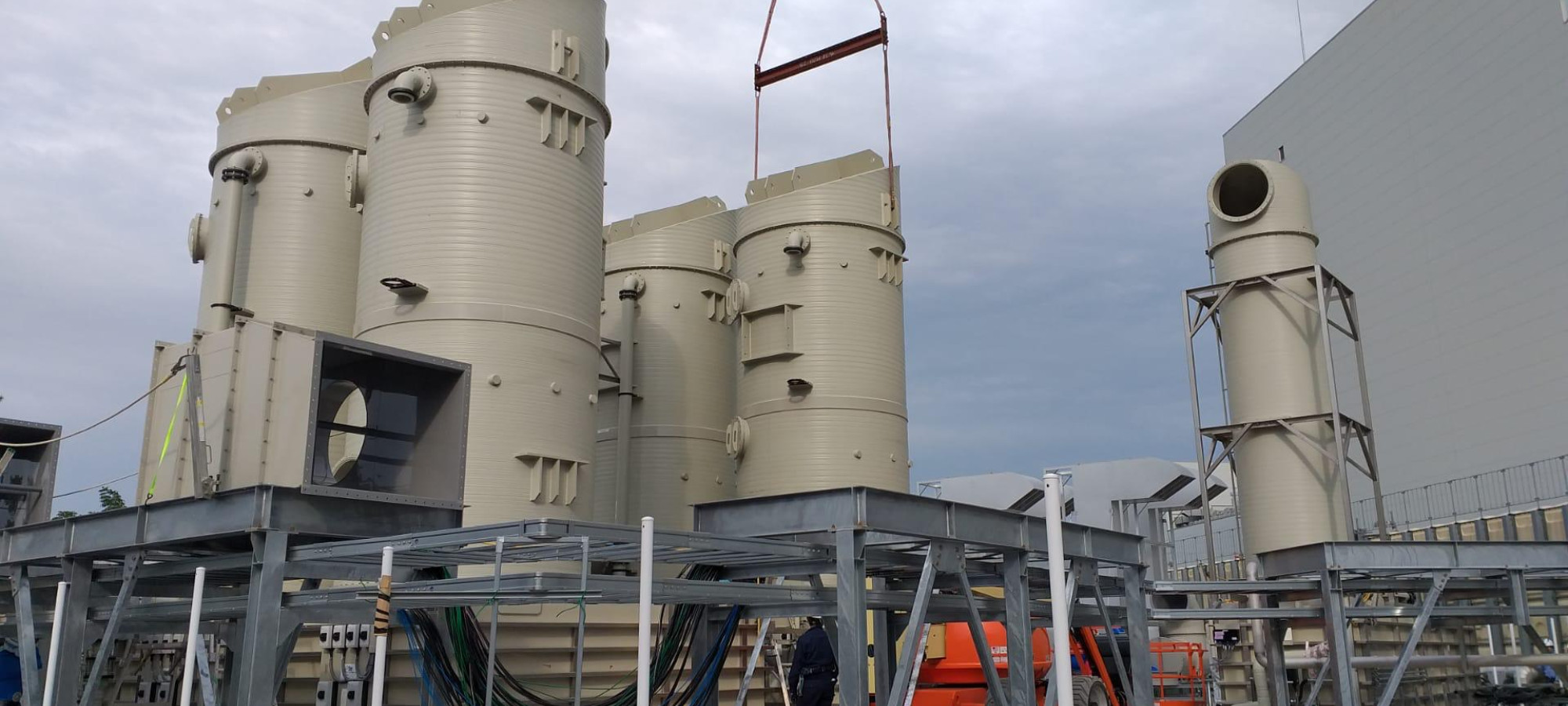
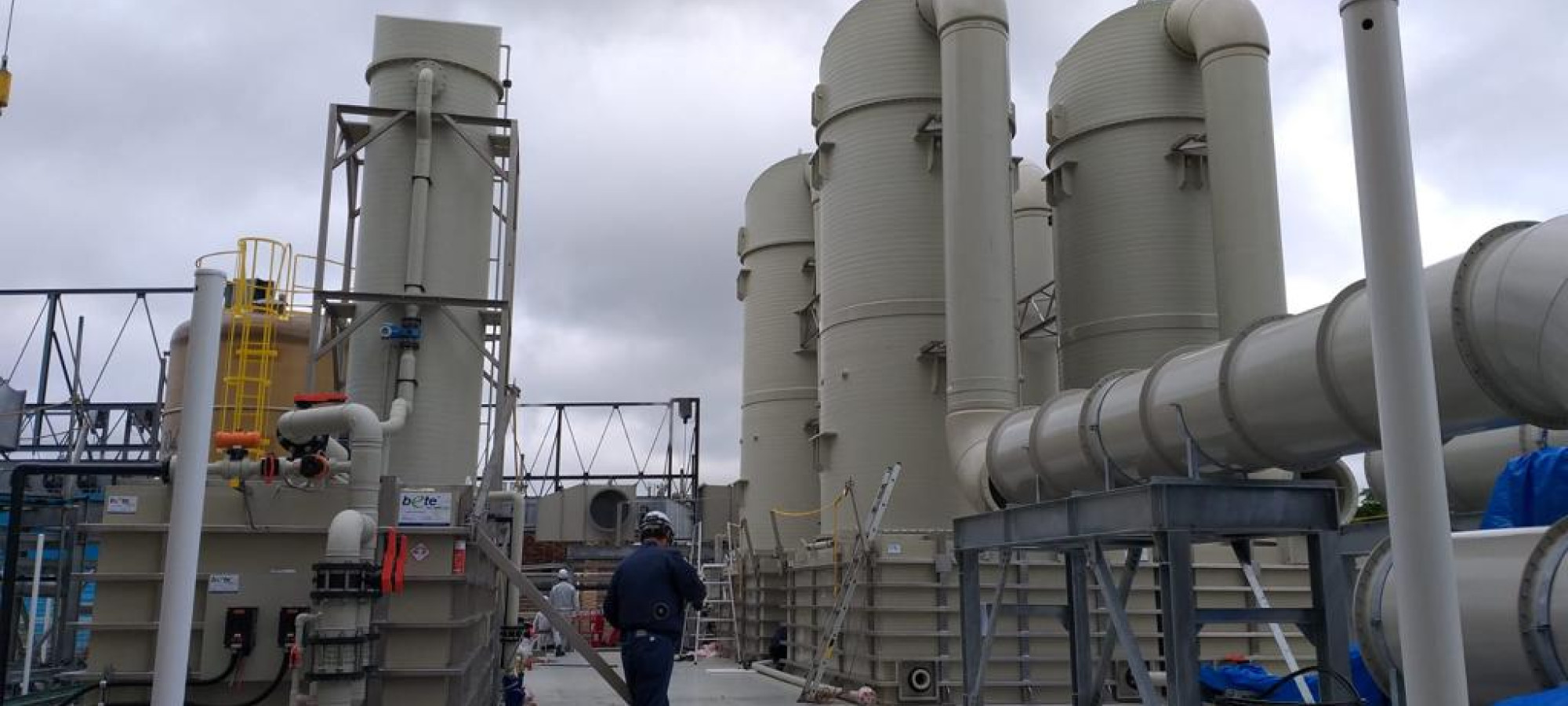
Gerelateerde projecten
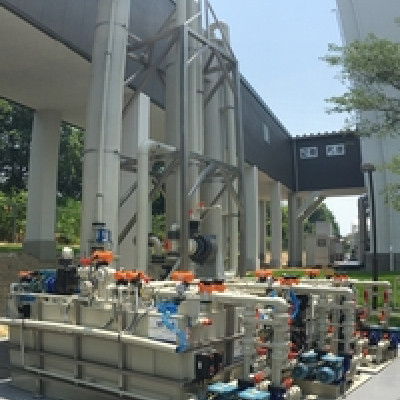
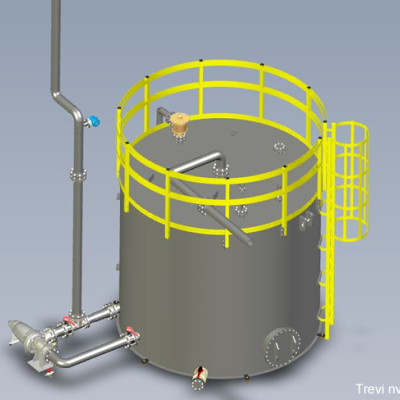
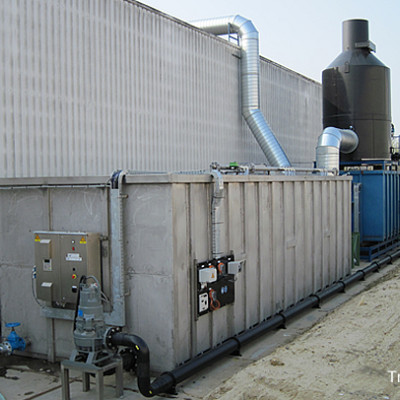